Dear Table 1, I know you’re there to help protect the health of concrete workers around the country, but you’re awfully confusing at times. Just tell me when you need a HEPA filter for Table 1 compliance already!
I imagine this is how just one of many letters we’d like to write to OSHA Table 1 might start—and it’s probably a little more civilized than some of us would like to be. Still, OHSA’s updated silica dust regulations went into effect on September 23, 2017, and the industry is still adapting.
Table of contents
A Quick Table 1 Dust Extractor Overview
One area that’s a major headache is what a dust extractor actually requires. Three major components come into play: CFM, filter cleaning, and HEPA filters.
First of all, we need to clarify that Table 1 covers most, but not all applications that create silica dust. For those applications not covered in Table 1, you also have Objective Data and monitoring options available. Companies like Bosch give you nice dedicated compliance websites to see how their products line up.
Table 1 is clear when you need a dust extractor with a filter cleaning mechanism. Another point to clarify is the term “filter cleaning mechanism.” It doesn’t have to be automatic like most dust extractors have – though that feature is nice. It can be a manual cleaning system like we see on many onboard rotary hammer extractors. The goal is simply to be able to clean the filter without reintroducing the silica dust you collected back into the air. However, some applications allow for just a cyclonic pre-filter system and not a cleaning mechanism.

Calculating the Required CFM for Dust Extractors
For CFM, the easy equation is that you need 25 CFM for every 1″ of grinder wheel you’re using.
Let’s do the math for a 5″ grinder:
5″ x 25 CFM = 125
A 5-inch grinder requires a dust extract with 125 CFM of suction. Simple.
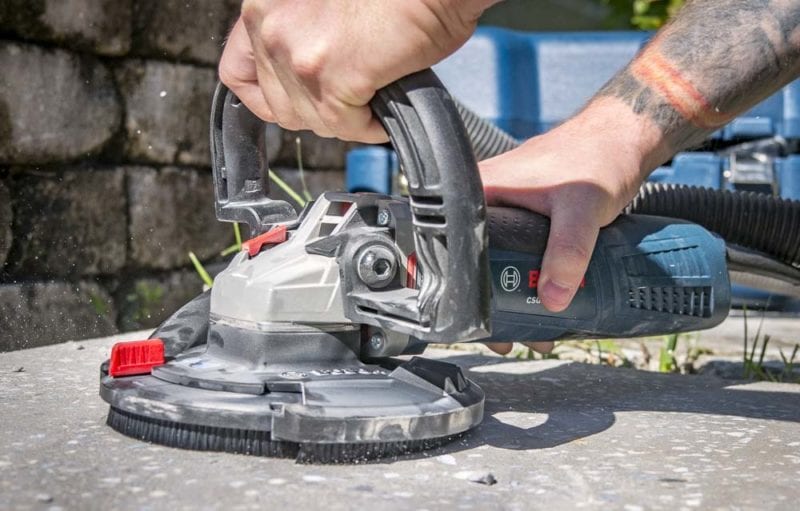
In most Table 1 applications, the filter requirement is that it “has a filter with 99% or greater efficiency…” Guess what? That’s not a HEPA filter. HEPA filters collect 99.97% of all particles 0.3 microns or larger. That exceeds the OSHA minimum requirement. While you need to check to be sure, most dust extractors come with a filter that already meets the 99% requirement.
When You Need a HEPA Filter for Table 1 Compliance
Table 1 requires a HEPA filter for two types of applications only. Hole cleaning and surface prep with grinders or walk-behind machines. That’s it. Here are the applications as stated in Table 1:
(vii) Handheld and stand-mounted drill (including impact and rotary hammer drills)
OSHA requires a HEPA filter only for hole cleaning. Otherwise, you simply need to use a drill equipped with a commercially available shroud or cowling with a dust collection system. Be sure to operate and maintain the tool in accordance with the manufacturer’s instructions to minimize dust emissions. The connected dust collector must provide the airflow recommended by the tool manufacturer, or greater. It also needs to have a filter with 99% or greater efficiency as well as a “filter-cleaning mechanism’. That filter-cleaning mechanism can be automatic or manual.
This section only requires the use of a HEPA-filtered vacuum when cleaning holes.
(xiii) Walk-behind milling machines and floor grinders
Use of a HEPA filter is required for indoor or enclosed space use if you’re not using a water delivery system for dust control. When using these tools indoors or in enclosed areas, OSHA requires a HEPA-filtered vacuum to remove loose dust in between passes.
And that’s it. You find only three mentions in all of Table 1 and two types of applications.
But There’s a Way to Stay in Compliance and Use HEPA Filters Even Less
For the two hole-cleaning HEPA applications, there is a way to do it without using a HEPA filter. When you’re using an ICC-approved chemical installation method for anchors, using a hollow core drill bit like the Bosch SpeedClean eliminates the need for a HEPA filter. You’re extracting the dust at the point of creation so you don’t have to blow the hole out.
Some Final Thoughts
You can still use a HEPA filter in all applications. It meets the requirements of 99% efficiency or better. You just don’t have to for most applications. In fact, you may be better off not using them when you don’t have to. Many tools suffer a performance drop when using a HEPA filter. On top of that, HEPA filters cost more to buy.
Hop[efully, this gave you better information on when you need a HEPA filter for Table 1 compliance. The goal is to work safely and effectively. You want to follow the rules and stay safe, but you don’t want to lower the efficiency of your dust collector or necessarily use HEPA when you don’t have to.