If an angle grinder is part of your daily grind, you’ve probably noticed the tool’s rapid shift from corded to cordless. Whether you’re new to the trade or a DIYer, you may be wondering the different angle grinder uses and if cordless is a legitimate option.
I jumped on a call with Kevin Gee, Senior Product Manager at Milwaukee Tool to take a closer look at this indispensable tool.
Table of contents
Angle Grinder Uses are Based on Size and Trade
Angle grinders are segmented into three major classes by wheel diameter: small at 4-1/2 to 5 inches, medium at 6 inches, and large at 7 to 9 inches. The motor size increases in these classes from 11-amp, to 13-amp, to 15-amp.

Cordless grinders simply ask more from their battery. In Milwaukee’s case, their High Output batteries give them all three classes on one cross-compatible battery system.
A Pro might simply prefer one size over another, but that’s not the only consideration. If it was, the vast majority of grinders would probably be 4-1/2- to 5-inch models since they are the smallest and lightest. But that’s not the case.
Why the Size of Your Angle Grinder Matters
Milwaukee’s research shows that MEP (mechanical, electrical, and plumbing) contractors usually prefer small angle grinders. These 4-1/2 – 5-inch grinders are well-suited for the MEP Pros’ occasional use. When the job calls for a grinder, the task typically takes a short time. So it’s not an everyday tool. The relatively few MEP guys that use a grinder frequently often opt for a 6-inch model.
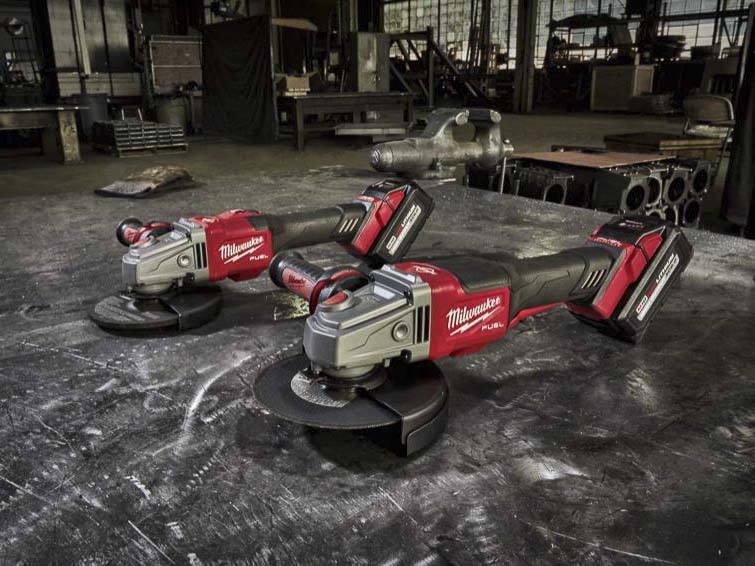
6-inch grinders are the tool of choice for fabricators who need to grind every day. These Pros need to clean up welds, make cuts, and other tough grinds. The medium angle grinder class has the power for these tasks whereas the smaller ones don’t have the fortitude.
It’s not unusual for fabricators to have at hand several grinders of different sizes, switch styles (paddle or slide), and attached accessories. These Pros get a big productivity boost by just grabbing the pre-loaded grinder that’s best for the job instead of switching wheels with every task. It also helps that they’re doing their work in a shop rather than moving from jobsite to jobsite.
Large angle grinders are in the realm of shipyard and oil/gas pipeline Pros—in other words, every day, all-day grinding work. These grinds and cuts take longer. Pros want them to remove as much material as quickly as possible and change wheels less often. Furthermore, these grinders can be bigger because these tasks aren’t usually done in small spaces like those done by MEP or fabrication Pros.
Many large angle grinders accommodate both 7- and 9-inch wheels, but some are dedicated to one diameter. Pros generally seem to prefer 9-inch grinders here in the U.S. while the global market trends toward 7-inch wheels. Part of that is preference and part is simply which diameter wheels are easiest to get hold of.
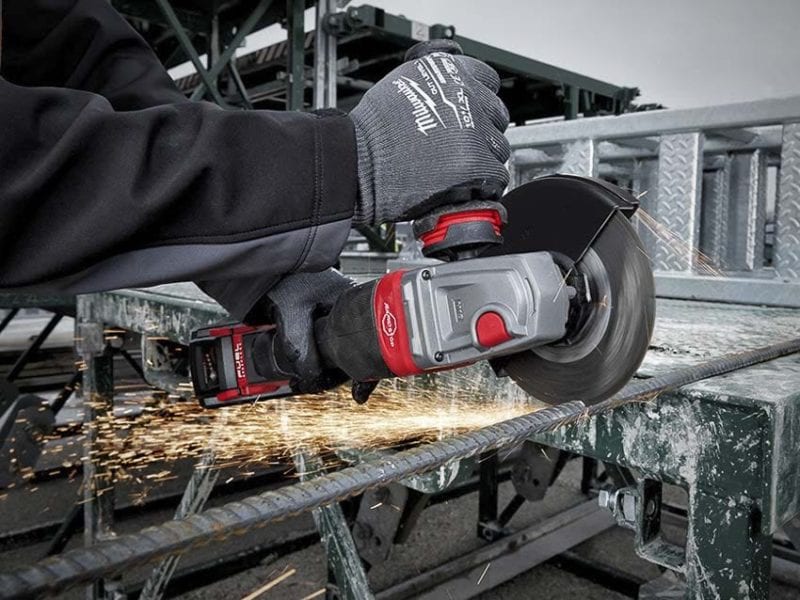
Cordless Grinders vs Corded
Angle grinders are cutting the cord along with nearly all major power tools. Of course, there’s still a runtime trade-off: fabricators and oil/gas pipeline Pros must have multiple batteries charged and ready to roll to work all day. It’s a huge convenience to not have a cord dragging behind you but you still need the runtime to complete the job.
Even so, Milwaukee is seeing a remarkable adoption of cordless angle grinders across all size classes. Angle grinder uses for work like boiler rooms, inside large diameter pipe, and confined spaces are safer and easier without a cord.
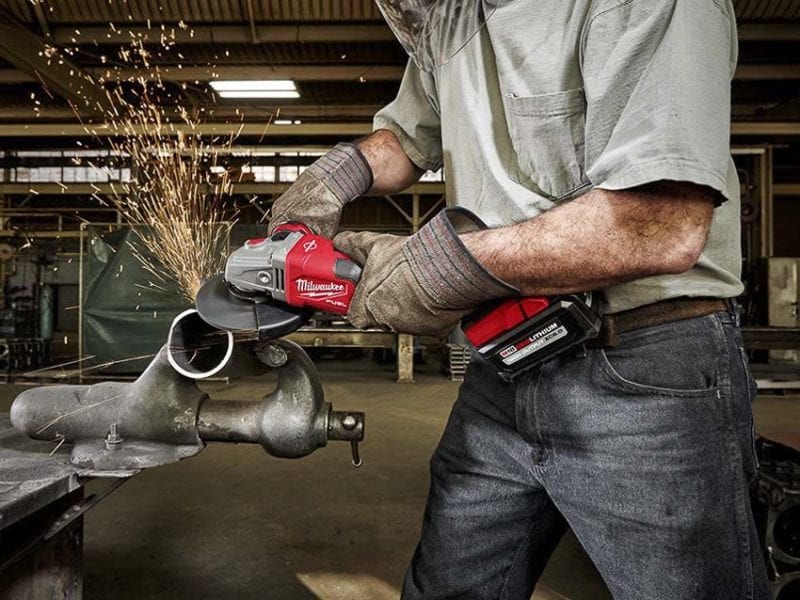
It’s no surprise, Kevin told us, that Pros want cordless tools that mimic the power and runtime of their corded counterparts. Less obvious, however, is that they want a corded feel in a cordless package: a cordless grinder should spin up like a corded one.
Cordless angle grinders don’t stray far from their corded design foundations to keep that familiar feel. However, some consistent feedback is that cordless models balance better because the battery and motor weights are on opposite sides.
Interestingly, Milwaukee can program its cordless grinders to spin up faster than a corded tool. It’s not that corded grinders spin up slowly, but they’re maintaining the feel for cordless.
Expect to pay a bit more for cordless grinders than you will for the corded versions. Just keep in mind that you’ll likely need a heavy gauge extension cord long enough to reach the nearest outlet. A flimsy and/or long cord can result in a voltage drop, especially with 15-amp grinders. By the time you add up the cost of cords and (possibly) generators, the cordless premium might very well disappear.
Braking Grinders Utilize New Motor Technology
An angle grinder’s wheel brake protects the workpiece, the operator, and co-workers in the area much like a circular saw’s brake. It’s critically important since a dropped grinder’s wheel can shatter, sending shrapnel through the air. Milwaukee engineers brakes to bring the grinder’s wheel to a stop in two seconds or less on small and medium grinders. It takes slightly longer for a 9-inch wheel to stop due to the mass and centrifugal force.
Rather than use clutches to stop the wheel, many brushless angle grinders rely on motor electronics to do the work. It creates a remarkably consistent safety system and so far, we’ve been impressed. It also eliminates having to replace worn-out clutches—which, to be honest, rarely happens.
Surprisingly, wheel brakes are not standard safety features and are not yet an OSHA requirement. However, larger, more advanced construction sites and government projects already require contractors to use braking grinders. If you’re bidding on a job as a subcontractor, make sure you check to see if there’s a braking requirement.
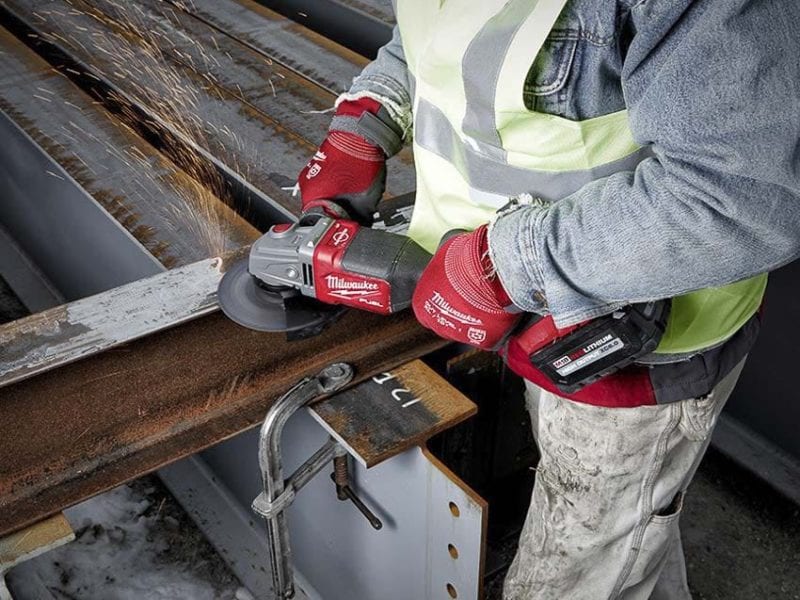
A safer work environment isn’t the only benefit of a wheel brake. Believe it or not, all those seconds saved not waiting for an un-braked grinder to slow down can add up to real productivity.
What’s Next for Angle Grinders?
Milwaukee expects cordless grinder adoption to continue its march forward and is staking new products on that expectation like a 6-inch grinder to supplement their small and large models. Kevin and his team are committed to understanding the entire workflow and process of grinder operators across the size classes. Their goal is to continue making improvements to their grinders and other cordless tools so you’re more productive from start to finish.
We also talked about using Milwaukee One-Key with grinders. For now, that functionality remains limited to tool tracking and inventory. Most Pros who use variable speed in their grinding want a physical dial on the tool, not controls in an app.
Cordless technology has improved, but it’s not good enough for every day use in a fabrication shop. Corded grinders are still king for most welders. And I agree with other comments that Metabo is generally the #1 brand in angle grinders. Not sure why they were left out of this article.
they need to make a cordless 4/5 inch variable speed they would sell like crazy in the tile trade.oh and no stupid paddle switches either i understand the safety reason but all the do is impede the user flexibility with it!
Milwaukee fuel playing up within 6 months of using it…..Dewalt, I’ve had since 2012 , not brushless
and still going strong!
The only down side to the cordless grinder is that it has helped increase the number of break-ins and theft of tools from job sites probably 100x
Why is this a Milwaukee ad? Several companies make cordless grinders, and Metabo is the king of angle grinders, hands down.