While Festool may have announced the Conturo Edge Bander back in February of this year (2015), nothing compares to taking closer look at this revolutionary new tool and seeing just what sets it apart from other products in the industry. We got to visit Festool in Germany and take a look at the process involved in developing the new Conturo Edge Bander, as well as the actual Festool manufacturing facility where some of these products are made and even Rainer joinery—a local shop using the new Conturo for select projects.
Festool Conturo Edge Bander Development
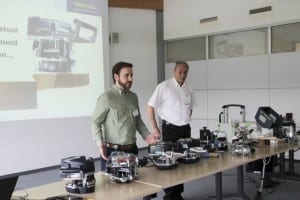
Having spent some time looking at Festool company history, we had some time to listen to Wolfgang Reines, who heads up the Edge Bander project (his first product with Festool was the well-regarded Domino). While there’s no standard approach or formula to how Festool generates ideas, they tend to look at the market and also combine that with the knowledge of their experienced product managers (Wolfgang was formerly a joiner, for example). The edge Bander was developed to compete with some handheld edge banders that were already on the market but which weren’t as capable and—quite frankly—looked like prototypes. They cost anywhere from $10,000 stationary solutions to $200,000 CNC-style machines. On top of that, the gluing stations cost another $50,000. Because of this, the market allowed Festool to develop a handheld solution that could accomplish the job of a larger system with the convenience of existing hand systems—but with greater capability and efficiency.
The Case for the Festool Conturo Edge Bander
Most inexpensive iron-based solutions cannot handle thicker edge bands. Glue edge band systems also are limited to thin edge bands and cost around $400. Since 2002, hand edge banders were developed which handled thickness of up to 3mm and cost around $2,000. This is the market Festool specifically looked at when developing the Conturo (their entire kit retails for around $3,200, though you can purchase it in various configurations).
Working with students in universities of applied sciences, they looked at strengths and weaknesses of existing solutions and also how the current edge banding systems and tools are operated. General observations were that these tools were heavy, and lots of adjustments were required (and buttons and controls to make these adjustments—there were tons of settings). The separate glue system was also inhibitor and created a lot of heat (burnt fingers were not uncommon).
Another observation made was the melting point of the glue. A higher melting point (Festool use 190º on the most common glue cartridges) allows for the furniture or piece to be out in then sun without an issue with the glue melting or losing integrity. The adhesive color shift was also an issue, and the machines themselves also became difficult to clean after a relatively short amount of usage. In a nutshell, there was a place in the market for a cleaner, more efficient, more user-friendly solution.
Developing the Festool Conturo Edge Bander
After making all of these observations, Festool had a good idea of what they were after. They wanted a new type of tool that was “clean” to use—one that wouldn’t burn your hands. Also, there needed to be a new “non-beaded” cartridge system for glue that would allow them to use only what was needed. If they could develop a tool that didn’t require a glue circulation system, then it would be much cleaner. At the same time, work on ergonomics began so that the finished product would be user-friendly and practical.
The next challenge was to keep it to one technology as opposed to an electric system for the glue component and a pneumatic system for the edge Bander. A computer was needed to automatically calculate the levels of glue and how fast the motor needed to turn. This would minimize the adjustments needed by the user and more or less automate most of the features—feed speed, glue quantity per edge band thickness, and temperature would all be automatically controlled by the system. This is how the Festool Conturo works and what makes it such an intelligent system for the user (and what allows it to have only minimal controls during general use.)
During the prototyping phase, adjustments were made to further reduce size to accommodate enough glue to do a conference table in one job while optimizing the cartridge size. Festool also added an LCD display (the first ever in a Festool product) to inform the user of what was occurring with the tool (temperature, readiness, glue levels, distance remaining, etc). Balance, weight, and shape were refined next for further ergonomic advantages.
Editorial Note: One fun fact we found out is that Festool names their prototype tools after the most recently born child in the company. It’s a nice touch that seemed to fit well with this family-oriented organization.
Tackling Specific Issues
In revisiting how to best deal with heat, adjustments to the edge size needed to be configurable even when the tool was “hot”. To do this, Festool decided that, instead of adjusting the lower base, the Conturo would adjust the middle base via a single dial (the same dial used on its plunge routers), and it would let you set both thickness and height in a single step.
Accessories were also developed in addition to the Festool Conturo to allow for flush trimming and even complex 45 degree bevel edge banding applications. A custom draw knife was developed to let you perform final finishing on cuts and get that perfect edge. The entire system from beginning to end is provided as a total solution. The glue cartridges (at roughly $2 per cartridge) are also available in various colors and materials, including EVA glue, water resistant glue, and more.

In the Field at Reick Joinery
There is currently no stationary edge banding unit that handles beveled banding, so we were excited to see the Conturo tackle this at local Reick Joinery. After giving the Conturo the requisite 10 minutes or so to warm up, the LED readout turned from red to flashing red/green, to green and we loaded a piece of 2mm ABS. You load it by clamping the piece in tightly, then clicking it backwards two clicks. The display indicates a properly loaded piece. While you can just push the button and feed at the current rate of speed, the trigger adjusts the speed and lets you vary as needed for curved applications. When you hit the end, the machine stops.
Cutting was a matter of grabbing a Festool flush trimming accessory which worked very simply. Another accessory adds a constant band feed for when you don’t want to use individual pieces. An edge cutter/router leaves just a tiny amount of glue, so Festool provides a draw knife to handle the rest, including glue removal and final edge detail.

Festool has a very unique adapter plate that lets the Conturo integrate into a tradesman’s own table for setting up bevel and straight edge banding. When applying a 45 degree edge band, the primary handle is removed. A thick bottom on the tool protects your hands from any heat, so placing the tool into the adapter plate wasn’t an issue. A rear extractor port can also be used to carry fumes from the glue away from the user. This plate solves the problem of 45 degree edge banding and works with anything up to 65mm.
For inside corners, an additional accessory can be added to the Conturo to allow it to get all the way into the corner with an edge band and you simply follow it up by pressing the corner firmly into place.
By this time we had run out of glue, so we paused to add another cartridge—a process which involved pressing a button, waiting for the plunger to retract, opening the lid, dropping in the next cartridge, and closing the lid. Changing colors takes a few cartridges to run though to the next color (unless you’re going from black to white, which takes around seven). Since each cartridge only runs around $2, it’s a cost-efficient solution—particularly when compared to other systems on the market.
Editorial Note: Festool showed us a homemade Systainer-based dispenser for edge banding that we thought was a nice solution for feeding material. Also a not-yet-available vacuum pump allows both horizontal and vertical positioning of material for edge banding and other work.
Even when applying edge banding to an extremely difficult shape, the Festool Conturo can always run a piece of edge banding through itself, applying glue to the piece, and then you can use a manual process to set the edge band.
For anyone working with ply material or MDF to create furniture, the Festool Conturo is an exciting new tool that should really shake up the marketplace. It’s a tool that will really redefine how this work is done—perhaps not in serial applications, but certainly with craftsman who would like a more flexible, portable solution for attaching edge banding in their woodcrafting projects.
Festool Power Tools (USA) Festool