Since we cover so many concrete tools, we get a lot of questions about these from readers. We figured it might be a good time to answer the question of exactly how does a rotary hammer work. Hopefully, this article appeals to both tradesmen who use these tools daily as well as those who just love to understand technology. For our part, we love peering inside any tool to see how it works. Tools are often a lot more interesting on the inside than the outside—and this is certainly the case for rotary hammers.
Of course, the best information comes from the source. So, partnering with us to deliver the inside scoop is Trey Sklar, Power Tools Business Unit Manager for Hilti North America.
How Does a Rotary Hammer Work? We Ask Hilti
Pro Tool Reviews (PTR): As we understand it, Hilti has a pretty robust past with respect to rotary hammer tools. What’s the story on that?
Trey Sklar (Trey): Well, remember that the way you used to drill a hole in concrete was by using a star bit. This was basically a large bit that you would strike with a hammer, rotate, and then hit again. Eventually, you’d get a hole. The first-ever electro-pneumatic rotary hammer tool on the market about 46 years ago in 1967 was the Hilti Torna 765. What made the big leap forward was the electro-pneumatic, or EP, working principle. That’s the foundation behind the rotary hammer mechanism.
Hilti figured out how to make it work and put out the Torna 765 rotary hammer. Soon after, the TE 17 became the first EP tool that was broadly accepted in the market. You can imagine what happened when these new electric rotary hammers showed up on a job site where, previously, the drilling had been a very slow, manual process. Hilti was the exclusive manufacturer of these EP tools for about 10 years.
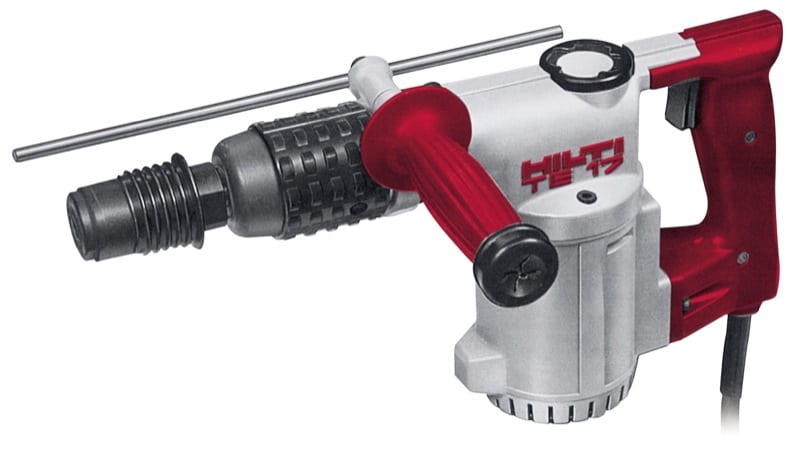
How Have Rotary Hammers Changed?
PTR: Talk about how rotary hammers have changed from Hilti’s first products until now.
Trey: As time has gone on, there were ways to remove weight from the tool. We learned how to take weight out of certain mechanisms by making them out of lighter materials. This allowed us to increase the power of the tool by redistributing the weight. For example, the TE 3000-AVR 65-pound demolition hammer has a striker weighing 4.9 lbs. This is roughly double the size of a striker in the same size class as most other manufacturers. This has been made possible by technological innovations and adjusting other areas of the tool’s natural mass.
The guide tube, where the piston goes back and forth, has also been switched out to some very advanced alloys. It lasts a lot longer than the original models. There’s now a much longer time between the maintenance periods. Hilti has also done things with the striker and the ratio between that and the piston that provided significant leaps in performance. Any more detail than that, and I’ll lose my job!
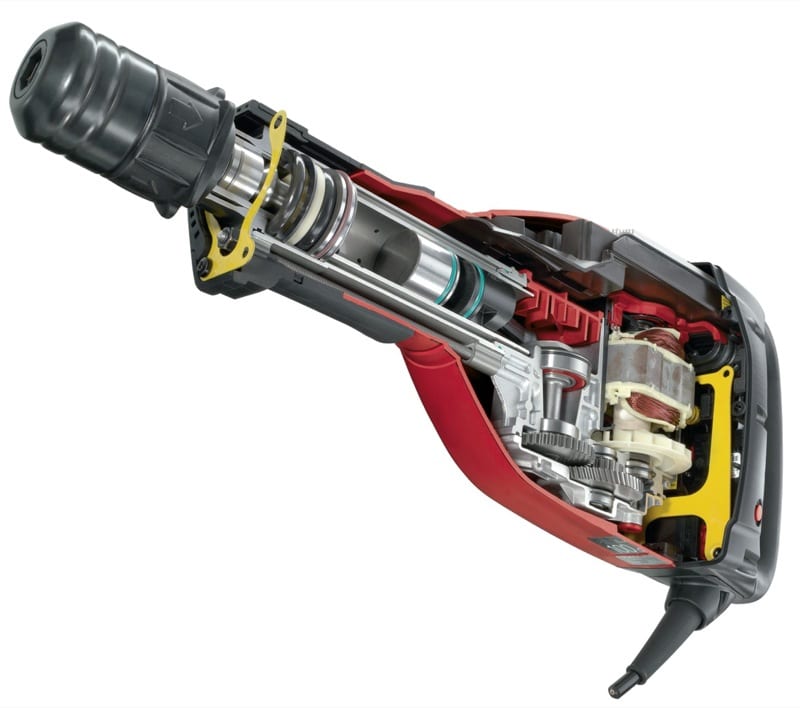
What About Vibration?
PTR: I won’t quote you on that…oh wait, I just did! What about vibration—how come these things don’t rip your arms off?
Trey: Vibration reduction is a natural result of the EP mechanism. It’s also an issue of safety and has, as a result, been an area that has gotten a lot of attention. Hilti has gone with a fully decoupled system. The rear handle on our AVR-equipped tools can move both up and down and from left to right in multiple-axis from the tool. Another area of concern is with regard to active torque control. Hilti uses mechanisms that add an additional layer of protection for the operator from an unintended sudden rotation of the tool body due to locking up on a piece of rebar.
What happens sometimes is that a contractor might hit a piece of rebar and jam. This could cause the tool to spin out of the user’s hands or even cause an injury. Hilti’s mechanism includes a magnetic clutch to disengage the motor when the tool body rotates more than 45 degrees in less than half a second. There is still a slip clutch in the tool, but this goes beyond that. This feature adds some weight to the tool, so it’s mostly located in the larger combi hammers like the TE 30-A36 on upwards.
The Difference Between a Hammer Drill (Cam-Action) and a Rotary Hammer (EP) Mechanism
Cam-action, or percussion, in a hammer drill gets you a light hammering on the concrete. It makes a really loud noise because the gears are physically rubbing against each other. You also don’t get as strong a hammer intensity. It’s because of this that hammer drills almost never have chisels, and they are never intended for 3/4″ bits.
The electro-pneumatic (EP) mechanism, on the other hand, uses a system where the drive piston and flying piston never touch. There is an air pocket between them, so you get a much stronger and more efficient transfer of power to the hammering mechanism. It also produces a lot less wear on the tool.
For more information, check out our article on hammer drills vs rotary hammers.
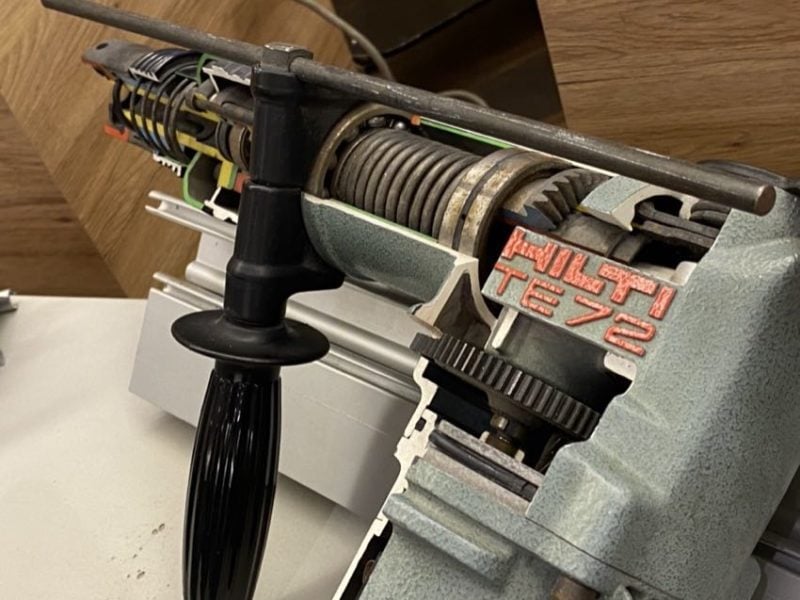
How Cordless Rotary Hammers Work vs Corded
PTR: What are the fundamental design and goal differences between Hilti’s corded and cordless tools?
Trey: Up until this year, cordless tools have been designed for optimal performance with 5/8″ bits or lower. So what you try to do is bring corded performance (or better) into a cordless model. In terms of the internal mechanism, there’s not a big difference or any really significant changes. You’re simply looking to get to that level where the mechanism is efficient enough to deliver a half-day or even a full day’s worth of work on a single charge.
Within the last few years, we’ve seen serial (repetitive) applications in certain size categories convert to cordless tools. These have reaped huge gains in productivity. You measure that by ensuring it drills enough holes per charge, and by ensuring those holes get drilled fast enough to meet the requirements to equal the corded tool. We’re now at a point where we actually have more cordless rotary hammer drills in our lineup than corded. We couldn’t do that unless those tools offered the performance of a corded tool.
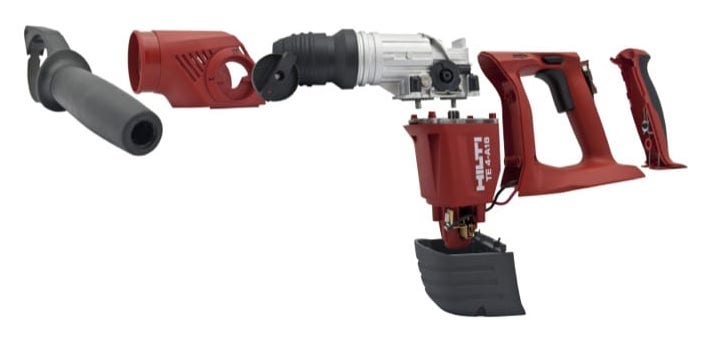
Obstacles in Design
PTR: What are the biggest obstacles in designing a great rotary hammer? Where are you constantly trying to improve?
Trey: Designing bigger tools that break the mold. For example, we’re getting into larger categories like the TE 30-A36. This is the world’s first cordless combi hammer, and it can handle drilling 3/4″ and larger holes. And the new brushless TE 3000-AVR demo hammer was designed to compete with the bigger pneumatics. Typically, what contractors have had to decide on is whether to use a less powerful electric tool or a more powerful compressor-driven jackhammer that has lots of vibration. We made the TE 3000 to deliver the power of a 60-pound air hammer in an electric tool that could run off a generator.
PTR: How do you test that to make sure you pulled it off?
Trey: Because of the impact power, we actually decided on industrial size railroad tracks. This is a piece of steel about twice the width of a conventional railroad track. Then, we basically beat the tool to death on it at multiple angles using a rig to run the tool until it dies. Beating a chisel against a railroad track is more abusive than even 10,000 psi concrete. The rig is really cool. It uses a robotic arm, operating the tool 24 hours a day with a chisel until it dies. Believe it or not, the steel actually yields after a while.
Breaking Down the Mechanics of a Rotary Hammer
Big or small, all rotary hammers are more or less the same in terms of how they operate.
- Pull the trigger or press the on/off button, and the signal is sent to activate the motor.
- The motor rotates, driving gears, rotating the bit and moving the piston.
- As the drive piston moves forward, the air pocket between it and the free flight piston is reduced in size. This creates a pocket of compressed air, which in turn pushes the free flight piston. The two pistons do not make physical contact.
- As the second, or free flight, piston moves forward, it contacts the striker.
- The striker, in turn, makes contact with the end of the drill bit or chisel, providing the hammer action.
The frequency of the piston cycle (hammering), is much higher than the rotary speed. This means the hammering action occurs numerous times for each revolution of the drill bit.
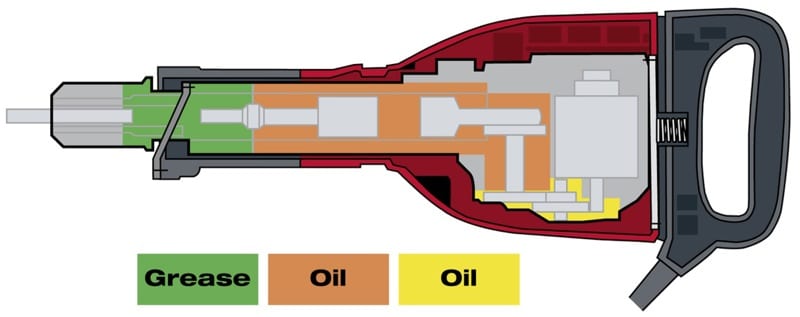
Room for Improvement?
PTR: Have we hit the pinnacle of what rotary hammers can do? Is there room for improvement?
Trey: There are some opportunities for significant enhancements in drilling speed for SDS-Max tools. We can also get more and more holes per charge on cordless SDS+ tools. Weight reduction is also going to be a significant factor. And one thing that we really tend to focus on is taking things that are mundane and revolutionizing them. We started that with the TE 17 of course. However, the TE 3000-AVR and our new hollow drill bits are other great examples that this innovation is still going strong. Corded drills have been all but replaced by cordless models. I think we’re going to also see cordless rotary hammers dominate the drilling of small diameter holes. Those corded products are going to go away for that type of work.
Wrapping Up How Does a Rotary Hammer Work
Thanks to Trey Sklar from Hilti for speaking with us and letting us pick his brain on how rotary hammers work. I would agree that we’re in the midst of a shift towards cordless for smaller diameter hole drilling. We’re keeping our eyes open to see what Hilti and others do on the bigger products as well.
If you are a product manager and have an interesting story to share about how a particular tool or technology works, please feel free to send us a note at info@protoolreviews.com. We’ll consider using it in a future article and contacting you to get more information.
Our company still runs a TE-17 and two TE-22’s. They are slower than new models obviously but great for any occasional drilling we get into. They just won’t die.
Realmente es asomobroso el funcionamiento de el rompedor TE3000 solo que hay muy poca informacion acerca de su funcionamiento, ademas que es execesivamente caro el mantenimiento, gracias por su atencion.
The TE 3000-AVR really is awesome. We have one and it’s always going out on job sites while the trailer compressor and air hammers stay parked in the shop.